Boiler Drain Valve Upgrade
Client:
UK Energy from Waste Power Station
Application:
Steam – 70 bar @ 415°C
Challenge:
ValvePro Limited were invited to a UK Energy from Waste Plant to meet with site Engineers to identify problematic Valves, offer replacements and help to reduce pressure on the Operations and Maintenance departments due to high levels of preventative maintenance during plant Operation. With our extensive Power Application experience, ValvePro were able to identify numerous leaking Drain Valves on the Client’s Main Boiler Drain Line due to the level of condensate collected in the Blowdown Pressure Vessel below. Upon further discussion with client, they advised that almost every Valve in the Drain Valve Bank (see Figure 1) had been replaced since commercial operation began three years ago.
Due to the nature of the Application, the installed Globe Valves were regularly being replaced during site’s warranty period due to leakage associated with Wire Draw across the Valve Sealing interface (see Figure 2). This issue is symptomatic of the Boiler Drain and Blowdown Application due to the frequency of operation, high velocity’s and Temperatures involved. To compound this issue, the valves that were originally installed were manufactured from materials with insufficient metallurgical properties to handle the application, with Hard Facing on the Seat only and the Disc material manufactured from 410 Stainless Steel.
Additionally, some of the Valves are in-accessible without additional scaffolding and meant that welding of replacement Valves into the pipeline was very difficult, not to mention the Costs associated with Cutting, Weld Prep, Welding into Line and NDE of all welds of the replacement Valves. This provided another challenge to ValvePro, to ensure that risks to the plant Operator’s is kept to a minimum during installation and operation.
ValvePro were tasked with collating the Operating Parameters, selecting the Correct Valve for the application and providing a Solution that would not only improve the operation of the Plant with a technically compliant product, but also remain competitive and provide a delivery to suit Client’s next planned outage, 10 working weeks from the initial meeting.
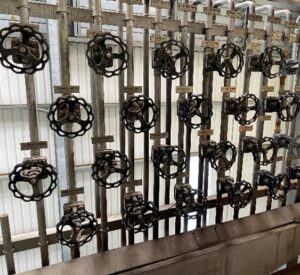
Figure 1: Existing Installed Boiler Drain Valves
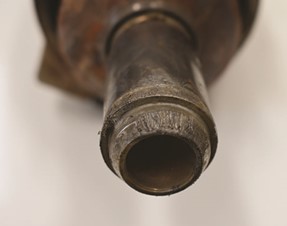
Figure 2: Valve Disc suffering Wire Draw
ValvePro Solution:
It is our mission to ensure that every Valve supplied by ValvePro is the optimum solution for the application. This measure requires taking into account all contributing factors, Operating Parameters, Location on Site, Frequency of Operation, Material Selection etc. and this occasion was no different. We believe that a quality Valve will in the long-run pay dividends when compared with a lower quality alternative such as the original product installed in this case.
Following a detailed review of the Application, ValvePro determined that the main contributing factor to the degradation of the Valve Sealing Interface was the lack of Hard Facing on the Disc. To combat this, ValvePro offered a Valve with Full Stellite® Faced Trim. This hard coating overlayed on base Steel increases the durability of the Sealing Faces and prolongs the service life of the Valve in operation. In addition, we offered Valves with forged 1.5415 Body and Bonnet Construction which are preferred to Cast Valves in High Pressure and Temperature Applications due to their refined grain structure, increased strength and resistance to porosity and shrinkage.
To provide a solution which solved all of the Site’s operational issues, ValvePro designed a ‘Drain Valve Assembly’ which comprised of two Globe Isolation Valves and connecting pipes so that the Drain Valves could be replaced quickly and efficiently, requiring only two on-site welds to the Inlet and Outlet Stub-Pipes (See Figure 3). Crucially, these Assemblies reduce the Number of Welds require to be performed on site during outage which reduces the on-site welding by 50% and saves the client costly Non-Destructive Examination (NDE) of the welds.
The Assemblies were also designed with plant operators in mind, allowing sufficient room between the Handwheel centres to safely operate the Valves without risk of fouling on the adjacent Handwheel. All dimensions were taken during our initial visit to site and required no further clarification during the quotation process.
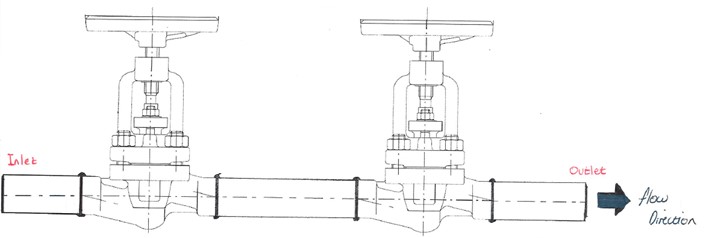
Figure 3: ValvePro Drain Assembly Drawing
Conclusion:
ValvePro Ltd were able to Design, Procure, Fabricate and Certify a solution within 8 working weeks that is both technically compliant and supplied at a price point that is competitive for the client. Furthermore, all parts were manufactured using acceptable Origin Materials with 3.1 Certification to support, thus meeting the criteria of the PS stringent requirements.
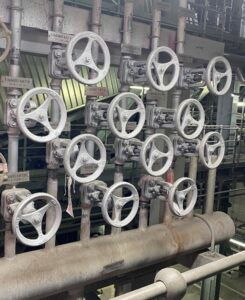
Figure 4:ValvePro Boiler Drain Assemblies Installed.