Replacement Obsolete Y-Type Globe Valve
Media:
HP Interstage Attemperator Feedwater Isolation
Challenge:
We were contacted by site engineers and were tasked to provide price and delivery for spare parts and replacement valve for a DN65 (2.5”) OEM Y-Type Globe Valve (fig. 1) that had a damaged stem and was inoperable via the existing Rotork Actuator as a result. As is procedure we set about looking for genuine replacement parts for the valve, but it was not long until we discerned that the valve in question was obsolete and therefore Spare Parts or a Replacement Valve was not going to be an option.
Having communicated this to the client we arranged a meeting to discuss options moving forward and introduce the Conval range of products. ValvePro Ltd are the Official Representative for Conval Inc. who specialise in Small Bore, High Pressure Globe and Ball Valves for Drain and Vent applications making them perfect candidates to replace the obsolescent OEM Valve.
Below are the main challenges we faced to ensure we provided a suitable replacement valve:
- Information on the existing valve was very limited, we worked from a drawing dated 1994 from the plants commissioning. We also struggled to collate information regards to Flow Rates, Pressures and Temperatures of the system meaning sizing the new valve was made more difficult.
- The OEM valve had an irregularly large internal seat diameter in comparison to industry standards. This posed a significant challenge as this effects the CV of the valve. We had to ensure that the CV would not be lower than the existing OEM valve.
- The valve in situ was restricted for space, meaning that the valve we supplied could not be more than 50mm longer in face to face and also had to adhere to strict height restrictions.
- Client requested an Electric Actuator be fitted to allow remote operation from the control room.

Figure 1: Original Valve drawing.
ValvePro Solution:
Working closely with Site Engineer’s to ensure all information provided was correct, we approached Conval to discuss the best solution taking into consideration all the parameters set by client. After much discussion it was agreed that the CAMSEAL Metal Seated, Severe Service Ball Valve would be the perfect valve to replace the obsolete OEM valve, providing an upgrade to the system by incorporating the following design features:
- In-line maintainability – Valve does not require costly and time-consuming cutting/welding on site due to the valve’s top entry design. Unique to the entire Conval range, routine maintenance can be carried out whilst the valve remains in situ.
- Zero Body, Stem or Seat Leakage – Due to the robust Stem-Ball Engagement, Patented Cartridge Design and Body/Bonnet sealing, traditional leakage paths have been precluded and validated with stringent testing.
- Positive Isolation – Due to the Ball design of the CAMSEAL, the risk of ‘wire draw’ fatigue of the Globe Valve Disc is removed. The valve will provide positive isolation for an extended period due to the design, in addition to this as standard Conval Ball/Seat materials are manufactured with durable Chromium Carbide Coating (<#1700) and from Inconel 718 as standard (>#1700), this ensures prolonged life in service.
To ensure that replacement would have no adverse effect on the piping system downstream of the valve, careful consideration had to be made to ensure that the CV of the replacement valve was equal to or greater than the valve that was to be replaced. However due to the space constraints on site this meant we could not fabricate ‘Pup’ ends to enhance CV of a standard Valve and thus we explored the route of flaring the internal bore of the Valve to achieve required CV. Working closely with the Conval Engineering department we were able to increase the CV of standard valve from 80 US Gal/Min to 125 US Gal/Min, significantly higher than the 100 US Gal/Min CV value required of the existing valve. The valve supplied was also the same face to face as existing unit thus ensuring no expensive pipe modifications needed to be made.
As per client request, ValvePro Ltd were able to Size, Source and fit Rotork IQT1000 Quarter-Turn Actuator to allow remote operation of the valve from Power Station Control Room.
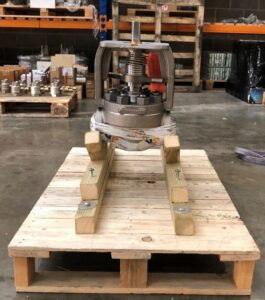
Figure 1: CAMSEAL Ball Valve before actuator mounting.
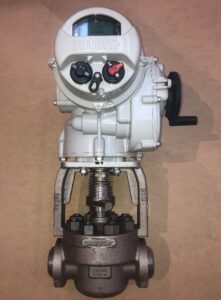
Figure 2:
CAMSEAL Ball Valve complete with Rotork IQT1000 Electric Actuator.
Conclusion:
ValvePro were able to Size, Procure and Supply a technically superior alternative to the obsolete OEM Y-Type Globe Valve with Conval CAMSEAL Metal Seated Ball Valve – a specialist in severe service design. We were able to negate the challenges of posed by the Overall Length and Large CV Value by Forging a brand-new body and machining the internal bore larger than standard to increase the CV Value to 125 US Gal/min. Similarly, through working closely with Valve Actuator supplier Rotork we were able to supply the correct actuator based on the Torque Figures of the CAMSEAL Valve, fit the actuator to the valve and supply complete unit ready to be installed on site, making it simple for client to fit the valve and hardwire the actuator to their control panel with ease.
In addition to the above, ValvePro were able to support client outage requirements and supplied the complete unit within 10 working weeks to accommodate strict client shut down, whilst remaining competitive and responsive to client requests.