Upgrade of Globe Valve to Conval CAMSEAL Metal Seated Ball Valve
Client:
UK – 895MW CCGT Power Station
Application:
HP Interstage Attemperator Feedwater Isolation
Media:
Superheated Steam – 253 bar @ 400°C
Challenge:
ValvePro were approached by the Mechanical Engineer at a UK CCGT Power Station experiencing issues with their existing HP Interstage Attemperator Feedwater Isolation Valves which were continuingly failing after being replaced. The existing T-Pattern Globe Valves had been replaced on a number of occasions since the site was commissioned in 2010 and the client wanted to upgrade the Valves to a long-term zero leakage Valve solution.
Responding to the ever-changing Power requirements of the UK Grid means that many CCGT Power Stations in the UK which were designed for ‘base load’ or constant running, are now being operated under an on/off or ‘Dual Shifting’ regime whereby the plant can go from idle to full load in a matter of hours, or quickly increase output to meet demands at busy periods of the day. This dual shifting pattern and rapid heating / cooling increases the thermal stresses on Valves and other process equipment designed for base load. Additionally, the increased frequency of Operation on Start-up causes further damage to the downstream Attemperator (de-superheater) Control Valves as High Pressure Wet Steam causes erosion of the Internal Trim components.
ValvePro were tasked with reviewing the site historical Operating Parameters, understanding operational shifting patterns and proposing a Valve solution which would provide Zero Leakage Isolation with an upgraded Design and Metallurgy to ensure improved longevity in service. See below example of Dual Shifting Plant vs. Base Load Operation:
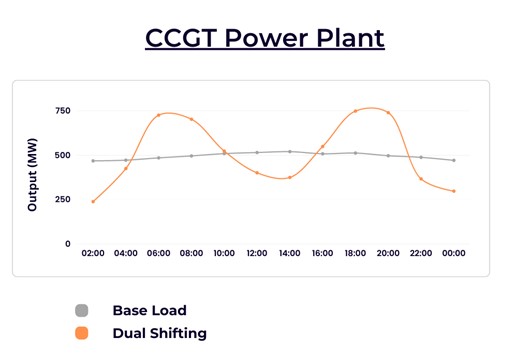
ValvePro Solution:
The existing 3” T-Pattern Globe Valve was experiencing a number of issues due to the dual shifting nature of the plant. Having undertaken a detailed review of the information provided by site, noted the issues they were facing and evaluated the Valve which was currently installed, it was clear that the Conval Camseal Metal Seated Ball Valve would be a superior upgraded Valve for this application.
The first consideration when replacing Valves is the Materials of Construction and the method of manufacture utilised to produce the Body and Bonnet. Typically, Valves > 2” utilise Cast bodies as the process offers commercial advantages over Forgings. However, if a plant is operated on a dual shifting regime, Forged valves are less susceptible to Thermal Fatigue and are mechanically stronger due to their superior grain structure uniformity, integrity and density. For this dual shifting, high cycling application Conval Camseal Forged Valves are perfectly suited.
The existing Valves were installed in a 3” Pipe and as such the Valve was also 3” with Butt Weld Ends. T-Pattern Globe Valves have an ‘Under/Over’ flow path, the Conval Camseal Metal Seated Ball Valve has a smooth un-obstructed Flow Path through the Valve bore across the Seats. The Globe Valves flow path induces a larger Pressure Drop (ΔP) across the Valve and thus negatively impacts the CV of the Valve. Taking this into account, we were able to offer a DN50 (2”) Valve which would offer a Larger CV than the existing Valve, whilst offering a commercial saving over a 3” Valve. Furthermore, to ensure no pipe modifications had to be carried out, this Valve was supplied with 3” Butt Weld Reducers welded to the Inlet and Outlet of the Valve to meet the face-to-face of the existing Valve to fit the space left when the failing Valve was removed from the line.
- Existing 3” T-Pattern Globe Valve CV: 49 US Gal/Min
- Conval 2” Camseal MS Ball Valve CV: 71 US Gal/Min
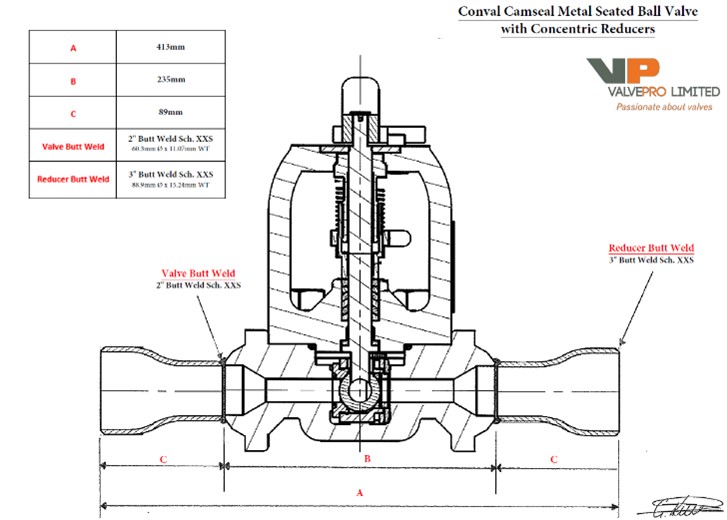
Figure 1: Ball Valve Sketch.
Increased Valve CV equates to quicker Plant start-up time, a significant advantage when operating the Plant under a Dual Shifting regime.
Due to the increased number of Operations (Valve Closed to Open) the Valves are subjected to, the Valve Disc and Seat sealing surfaces are increasingly exposed to potential wear by the arduous application and may fail prematurely due to severe damage to the sealing surfaces. In this case, the existing Valve Seat and Disc material was Stellite 6 overlayed onto Stainless Steel base material – a very common combination of materials for Valve internal trim components. It is worth noting that Stellite internals are suitable for General Service Valves, operating in-frequently in on/off applications.
Conval Camseal Ball Valves are manufactured with Inconel 718 Ball and Seats which are Chrome Carbide Coated using HVOF process, creating a Mechanical bond between the base material and the extremely hard coating. From a hardness perspective, Stellite 6 has a Rockwell Hardness value of ~37 HRc, whilst Conval’s Camseal Ball Valve Chrome Carbide Coated Trim has a Surface Hardness of ~70 HRc. In real terms, the increased Hardness and un-restricted flow path a Ball Valve offers results in prolonged service life in Severe Service applications.
Gland Sealing and Body to Bonnet Seal areas commonly experience failures when exposed to severe Thermal Stresses. Standard Gland Arrangements (see Figure 2) utilise a Gland Follower to compress the Packing Rings when two Gland bolts are Torqued down. In addition to this, the use of ‘Floating’ Backseats installed into the Packing Gland as a means to protect the Packing area are nullified if the Gland Follower is providing uneven load on the Packing Area. These Floating Backseats are generally Stainless Steel (AISI 410), or Stellite Overlayed in higher Pressure Valves – this also susceptible to de-lamination to expose the base material. This combination, whilst widely used can lead to uneven load exerted on the Packing Rings and thus exploit a potential Leak Path through the Gland.
Conval’s proprietary solution to this phenomenon is their Integral Gland Wrench (IGW) – see Figure 3. This innovative design ensures an even concentric load on the Packing Rings to prevent un-even load and the Leak Path therefore generated. The IGW allows slight adjustment in-situ and ValvePro can supply the correct Wrench’s from UK Stock. Additionally, Conval’s Backseat forms part of the Bonnet Assembly and is manufactured from Solid Cobalt Alloy and is not susceptible to de-lamination. This robust Backseat arrangement, coupled with Conval’s superior Gland Arrangement ensures reduced risk of Gland Leaks when the Valve is in operation. Should your application have severe vibration or risk of Fugitive Emissions, Live Loaded Packing can be installed to the Integral Gland Wrench (IGW).
Actuator
The existing Globe Valves were fitted with Auma Multi-Turn Electric Actuator which are set up for a long travel, rotating through 360° to operate the Valve. The Camseal Ball Valve solution that ValvePro offered as an upgraded Valve is Quarter-Turn by design and has no Linear Thrust to consider, only Torque through 90°.
As such, ValvePro worked closely with the Actuator Manufacturer to ensure the best Technical and Commercial solution was reached for the End User. To this end, we supplied the Gear Casing to suit our Valves only, with the Control unit part of the Existing Actuator able to be retrofitted on-site once the existing Valves have been cut from the line. By doing so, ValvePro were able to achieve a 50% reduction in Actuator price compared with complete new unit cost and reduce the lead time to 2-3 working weeks as the Gear Casings are kept in stock in Mainland Europe.
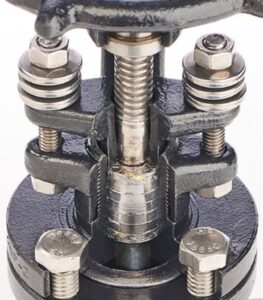
Figure 2: Standard Gland and Bonnet Arrangement
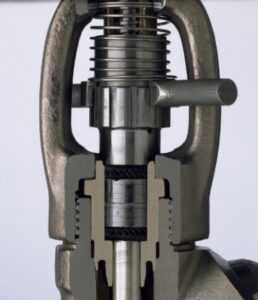
Figure 3: Conval Integral Gland Wrench (IGW).
Conclusion:
Utilising ValvePro UK Stock of Camseal Metal Seated Ball Valves and working closely with the Actuator Manufacturer, ValvePro were able to supply all components together as assembly (see Figure 4) within 4 working weeks to suit Clients Outage Shutdown dates. Additionally, ValvePro solution utilised a commercially competitive 2” Valve whilst increasing the CV when compared with the existing Valve and ensuring no pipe modifications were required to install the Valves.
ValvePro Scope of Supply included:
- 3-off Camseal Metal Seated Ball Valves – 7H Body
- 3” x 2” Concentric Reducers – Butt Weld XXS
- Welding and NDT of Reducers to Valve Inlet and Outlet
- Auma SAR Quarter-Turn Actuator Gear Casing (less Controls)
- 1 Hydrostatic Shell and Seat Test Certification
- 1 Material Certification for all Pressure Containing Parts
- Weld Procedure, Report and NDT Results
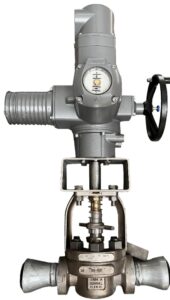
Figure 4: Completed Valve Assembly
Conval manufacture Forged Valves up to and including 4” (DN100) through a full range of pressure classes up to ANSI #4500 and materials including SA105, SA182-F22, SA182-F91, SA182-F92 and SA182-F316 Stainless Steel – specialist Urea grade materials and Exotic Alloys are also available on request.